Bronkhorst flow metering for low flows
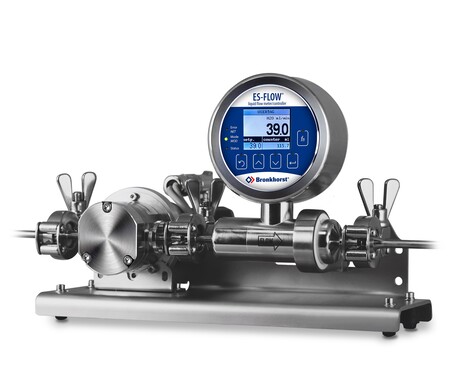
What do micro reactors, catalyst research and additive dosing have in common? They all require handling low-liquid flows.
In control and measurement, ‘low’ and ‘high’ flows are often arbitrary. At Bronkhorst, ‘low flow’ is our business.
For us, ‘low flow’ is less than 100 g/h and ultralow flows are below 5 g/h (100 g/h is equivalent to about 2000 water droplets/hour, while 100 drops is around 5 grams).
Where do we need accurate instruments for low liquid flows up to 100 g/h?
- Chemical catalysts: Low liquid flows of hydrocarbon compounds, at high pressure, are dosed at a stable flow.
- Biotechnology and pharmaceutical: Labs-on-a-chip and other microfluidic devices significantly reduce chemical use and experimental time.
- Odorising of gases: Injecting small but continuous amounts of liquid additive causes ‘warning’ odours.
- Where performance of an experiment is determined by measuring the correct amounts of liquid.
What is different about liquid flows of less than 100 g/h?
Laboratory-based low-flow applications involve phenomena not observed in, or not relevant to, larger flows. Due to the amount of liquid transferred, they are sensitive to even the tiniest disturbances in process or ambient conditions. Key is minimising the influence of external conditions on flow stability.
For example, a small leak of gases or liquids within the process can considerably influence the intended liquid flow; particles or contamination cause obstructions that can change the flow in an undesired way; and inconsistent pressures, excessive pump stroke pulsations and pressurised gases in a liquid all lead to instability.
Bronkhorst excel at optimising complex low-flow applications. An in-depth knowledge of fluid characteristics and system components in a wide range of circumstances ensures best practice.
Measurement options also help. Bronkhorst’s portfolio includes thermal-based, ultrasonic and Coriolis flow meters and controllers. All are suitable for low- and ultralow-flow applications. To reflect, a flow meter consists of a sensor that measures the medium’s flow rate; a controller combines that sensor with a control valve that controls the medium’s flow rate.
Reiterating, optimal performance requires much more than just an excellent flow meter/controller. By eliminating leaks and dissolved gases, keeping tubing volumes small, the flow controllers can generate a stable flow.
The different working principles offers choice. With thermal-based mass flow devices, a constant temperature difference is created along the flow tube. The energy needed to maintain that temperature difference while liquid flows is proportional to the mass flow rate.
For Coriolis flow meters, flow is through a thin vibrating tube, causing it to twist. The change in deflection is a measure of the mass flow. Interestingly, the change in vibration frequency of the flow tube gives the density of the product/medium.
When to choose a Coriolis flow meter/controller?
Most applications! Specifically, where absolute accuracy and stability are essential; where thermal sensitivity issues exist; where the product density needs to be monitored. Coriolis meters are useful on liquids with unknown properties. That said, Coriolis meters might need installation measures to reduce shock and vibrations.
When to choose a thermal flow meter/controller?
The economical choice. Specifically, where the fluids are stable (constant liquid density, viscosity, thermal conductivity and heat capacity); reproducibility is excellent; they generally have small pressure drop, which can help where there might be dissolved gas, helping to keep the flow stable.
Tips ‘n’ tricks
The following can be expanded but might help in respect to low liquid flows:
- Tip 1: Choose a flow meter that suits the process and conditions.
- Tip 2: Ensure a stable (inlet) pressure.
- Tip 3: Minimise the containment or dissolution of gas in the medium.
- Tip 4: Use piezo control valves on low flows.
- Tip 5: Minimise volumes between the flow device and process.
- Tip 6: Purge well before operation.
Advancing Precision and Reliability in Analytical Systems: Leveraging Valve Diagnostics for Optimal Performance
Bürkert Fluid Control Systems offers a sophisticated approach to optimising valve...
The Invisible Threat in Lab Water: Effective Solution for Microplastic Contamination
The Arium Pro VF system from Sartorius was put through tests to remove microplastic particles...
Environmental Monitoring in Regulated Life Science Sectors: Ensuring Product Integrity and Compliance Through Automated Climate Control
This article explores the necessity of climate monitoring and how automated systems — like...