Spray drying innovation is leading to significant efficiency gains
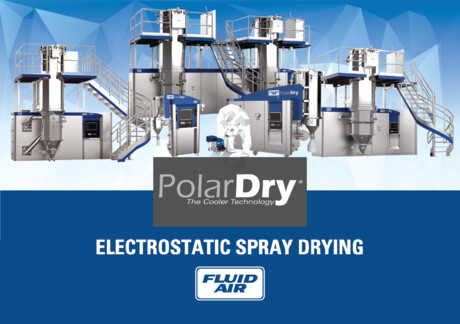
Fluid Air has introduced new spray drying technology to a range of Australian manufacturing industries, including pharmaceuticals. PolarDry Electrostatic Spray Drying (ESD) retains the biological activity of heat and oxygen-sensitive products after drying compared to more traditional extreme temperature spray drying methods.
“Fluid Air’s testing facility in Melbourne has advanced analytical capabilities to support our customers,” said Dr Akm Masum, Fluid Air’s Applications Scientist.
The Fluid Air testing centre is flexible, depending on the specific needs of the client, and they are ready to test your product for free to see if their technology can help you increase your efficiency gains.
“We dry at lower temperatures during electrostatic spray drying and cause less damage to the customer’s products than the alternative methods. This helps to preserve the bioactivity of heat-sensitive materials, such as microorganisms, proteins, dairy, bioactive materials and pharmaceuticals.
“Electrostatic spray drying uses low drying temperatures of around 90–150°C inlet and 30–60°C outlet. When compared to traditional high heat spray drying (150–250°C inlet, 70–110°C outlet),” said Dr Masum.
Do you dry your product with extreme heat? Contact us today to arrange a free trial of your product.
Celio Furquim is the Fluid Air Business Development Manager and said that because of the large capital investment customers make in the technology, Fluid Air was happy to offer some methods of free testing to show the technology’s capabilities.
“We are happy to work with our customers to ensure that business will be benefited as we know that these machines cost much money.
“We want to show everyone this technology is the future,” he said.
“The efficiency gains that it provides can be large, so we take that time because we have confidence in our product.”
Furquim used a simple recent example to help clarify how the technology works.
“We did a trial overseas at a company that makes lemons into lemons lollies, and they were drying the powder and normally at high temperature they would only get 8% of the lemon into the final confectionary product. When they did it with our product, they got about 70%. Lollies cost too little for it to be cost-effective but it is a great example of how our machines work and the results can be translated to range of different industries,” he said.
Dr Masum went into some more detail about what exactly that means for manufacturers and producers.
“There is a reduction in bioactivity with traditional heat spray drying technology. Whereas in our electrostatic spray drying technology there is almost no loss after drying,” he said.
“Also, when we store our products for longer periods, the bioactivity is maintained.”
Dr Masum said, “It all depends on the customer; if they have any specific testing requirement based on what we already have, we can do that. Our lab is fully kitted out. In addition to drying the liquid feed into powder, we also can analyse the liquid feed before drying and the powder properties after drying.
“We have almost everything that we need for powder characteristics. For example, we can measure the moisture content, water activity and glass transition temperature of the powder,” said Masum.
Scalable from R&D to Commercial Production
Furquim says that being scalable to any production size is a crucial feature. With a range of machines starting at an R&D level and moving up to total commercial products available.
“Any heat-dried or cooled product to create a powder, we can help. We have a Queensland-based customer that is making live biotherapeutic materials; they use our model 0.1 to test and validate results, before using our large model 4.0 machines to produce their products on a commercial scale.”
Contact us today to find out more about this revolutionary technology: phone 1300 079 998 or email sales@spray.com.au.
Fluid Air is a subsidiary of Spraying Systems Co.
The Balance That Takes Your Lab to the Next Level
Quintix Pro laboratory balances from Sartorius are designed with advanced features that enhance...
Simplicity is the Ultimate Sophistication in Nanoparticle Manufacturing.
Micropore Pathfinder offers a better way to produce nanoparticles. With customisable,...
Unlocking the Secrets of Intracellular Communication: NanoSight Pro Masters Extracellular Vesicle Analysis
The NanoSight Pro can be employed to explore various labeling approaches for unraveling different...