Towards greener labs with Thermo Fisher Scientific
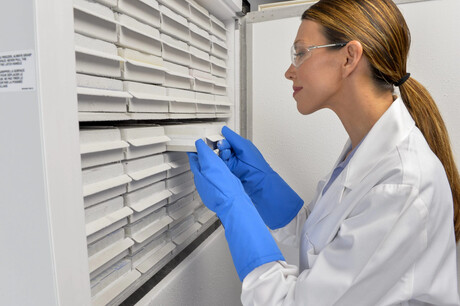
Labs, whether in academia and research or biotechnology and manufacturing, are all aiming to reduce their carbon footprint. A recent survey conducted by Thermo Fisher Scientific indicated that over 70% of respondents would like to go greener in the lab. The company is now achieving new innovative approaches in both thinking and manufacturing in its mission to make the world healthier, cleaner and safer.
The ACT label
Laboratory workers can opt for more sustainably conscious products through the use of the ACT label, created by non-profit organisation My Green Lab. This virtual label helps consumers make smarter and more sustainable product choices by providing a ‘score’ for each product that is labelled. The score is based on the product’s environmental impact with regard to its manufacturing practices, energy and water use, and end-of-life disposal, with an emphasis on accountability (A), consistency (C) and transparency (T).
Thermo Fisher Scientific was the first to ACT label its laboratory consumables — such as its Thermo ScientificTM MatrixTM storage and liquid handling products — in recognition of the fact that such consumables are often single-use and have a bad reputation when it comes to sustainability; the need to implement sustainability in the manufacturing of these products was therefore crucial. This is an example of how the ACT label has helped incentivise manufacturing and end-of-life changes for single-use consumables.
Energy efficiency
A 2015 study on laboratory energy consumption by the Center for Energy Efficient Laboratories (CEEL)[1] determined that laboratories can use over 800 GWh of energy each year — equivalent to the yearly greenhouse gas emissions from 122,200 passenger cars[2]. Indeed, a single ultra-low temperature lab freezer can use as much as 14,000 kWh of energy per year.
Thermo Fisher Scientific is committed to designing energy-efficient products that help power your work and support your sustainability objectives without compromising performance. For example, the company’s ENERGY STAR® certified ULT freezers are specifically designed and engineered for the safe use of green hydrocarbon (HC) refrigerants that are in compliance with the US Environmental Protection Agency’s (EPA) Significant New Alternatives Policy (SNAP) program, the European Union’s F-gas regulations and other regulatory programs. These hydrocarbon refrigerants not only help improve system performance, but they also do so with minimal environmental impact. They use 70% less energy and have been shown to operate 25–42% more efficiently than conventional-refrigerant ultra-low temperature units.
The Thermo Scientific TSX series ULT freezers also utilise a variable speed compressor powered by adaptive V-drive technology, designed to minimise energy consumption without sacrificing sample security. Rather than running continuously, the V-drive system operates like a car, accelerating and decelerating in response to usage and the environment, delivering the needed cooling capacity for the given situation and helping reduce the stress on the system. Units like those within the TSX series also output less heat, meaning they can be brought into the main lab area as they won’t make the surrounding space hotter. Furthermore, less heat output means less of a burden on the HVAC system, translating to lower energy bills.
The company’s SorvallTM centrifuge range meanwhile offers several key features that contribute to reduced energy use during operation. Sorvall LYNX 4000 and LYNX 6000 Superspeed Centrifuges have a Green Mode setting, which puts the centrifuge in sleep mode (idle) when not in use for more than two hours. The Smart Vacuum feature of the LYNX 6000 removes up to 80% of the air inside the centrifuge chamber, minimising air friction on the spinning rotor. The Sorvall BP 8 and 16, Sorvall BIOS 16, and CryofugeTM 8 and 16 models also include an energy-saving mode that shuts off the automatic cooling function when the instrument is not in use, and an Auto-DoorTM feature which shuts off the cooling system when the door opens.
Less waste
As a supplier of life science products, Thermo Fisher Scientific is focused on reducing waste and generating significant cost savings for itself and its customers. For example, the company has designed products such as the One Shot 50 mL FBS (foetal bovine serum) bottle, which generates 33% less waste than aliquoting from 500 mL bottles. Meanwhile, the company’s various manufacturing sites strive to divert at least 90% of their waste materials from landfill.
Fourteen of Thermo Fisher Scientific’s manufacturing sites in the US, the UK, Singapore, Germany, the Netherlands and Israel have been independently certified for zero waste, with audits validating that more than 90% of the nonhazardous waste from these sites is diverted from landfill. The company also aims to incinerate no more than 10% of its diverted waste, compliant with host government guidelines — though in the case of its Norway and Japan facilities, for example, incineration may be greater than 10% as these countries’ infrastructure supports waste-for-energy incineration on a large scale.
Sustainable packaging
The first rule of packaging is that it must protect the product — whether from the mechanical rigours of handling and shipping or extreme temperatures. Thermo Fisher Scientific aims to design packaging solutions that preserve product integrity while maximising freight density and therefore using less fuel. The company is also utilising technology that consumes fewer resources per reaction, redesigning the packaging of individual components within kits, reducing the use of dry ice and other cold shipping methods, and transitioning to more sustainable shipping materials.
Invitrogen ProQuantum immunoassay kits are one example: they use more sustainable packaging and offer less waste than a traditional immunoassay such as an ELISA. This is achieved through the assays’ proximity-based amplification technology, which allows researchers to detect lower levels of protein with lower sample input than traditional methods. With higher sensitivity and very low sample consumption, users not only can get the most out of their precious samples but also consume less plastic than other immunoassays. Furthermore, researchers can store four ProQuantum kits in the same space as just one traditional ELISA kit.
Another example is a new alternative for expanded polystyrene (EPS) coolers, which have for decades been the preferred external packaging for cold-chain shipments but have limited recycling options. Thermo Fisher Scientific has developed a 100% paper, readily recyclable cooler that meets the thermal and structural requirements necessary to uphold its stringent product quality standards, but with a smaller environmental footprint. The company encourages its customers to recycle these paper coolers alongside other paper and corrugate materials, and explore local recyclers for EPS foam coolers.
Less hazardous
Minimising hazardous materials and hazardous waste in the lab is a win for both safety and the environment. Fewer hazards can lower exposure risk for lab personnel and reduce costs for hazardous waste disposal.
By incorporating principles of green chemistry and green engineering into its product design, Thermo Fisher Scientific has created greener product alternatives that can help advance sustainability in the lab by minimising the use of hazardous chemicals, minimising waste and material consumption, and increasing energy efficiency. These products, which are signposted on the company’s website with a distinctive green leaf symbol, have been rigorously evaluated to ensure they meet at least one of the following criteria:
- Inherently less hazardous
- Reduces the need to use other hazardous materials
- Generates less hazardous waste
- Reformulated so as not to require Dangerous Good for Transport (TDG) classification
- Free of ozone-depleting substances
The company’s scientists have also developed a proprietary fluorescent resonance energy transfer (FRET) assay that helps to eliminate radioactivity in testing enzyme-based product lines. Replacing radioactive isotopes with a fluorescent dye has reduced radioactivity by 60% at its sites in Carlsbad, California, and Austin, Texas, making both employees and facilities safer. This new process has also allowed the company to execute assays in half the time and with more accurate results. This breakthrough has the potential to one day completely eliminate radioactivity in the quality control testing of many laboratory reagents.
Conclusion
The science of the global climate and environmental crisis has become a defining issue of our time, with life scientists rightfully expecting accountability from their suppliers and partners. Thermo Fisher Scientific is committed to improving its collective impact on the planet by introducing greener products, optimising resources and cutting waste in their mission of making the world healthier, cleaner and safer.
For more information, visit thermofisher.com
References
- Allison Paradise (2015) Market Assessment of Energy Efficiency Opportunities in Laboratories.
- US EPA Greenhouse Gas Equivalencies Calculator, http://www.epa.gov/cleanenergy/energy-resources/calculator.html. Accessed 03 December 2020.
RMIT Researchers Help Harness AI For Solar Cell Production
The next generations of solar cells may be developed with the help of this innovative technology.
University of Canberra Scores ARC Discovery Project Funding For Frogs
The multi-agency, multi-year project hopes to reintroduce the green and golden bell frog back to...
Sustainability in the Lab Concerns Us All
Whenever the topic of sustainability comes up in the scientific community, there are many issues...